Casting Aluminum 101: Necessary Actions for Newbies
Casting Aluminum 101: Necessary Actions for Newbies
Blog Article
Aluminum Spreading Solutions Unveiled: Crucial Insights and Tips
Exploring the world of aluminum spreading services can introduce a globe of complex processes and nuanced factors to consider that are essential for effective results. As industries significantly turn to light weight aluminum for its lightweight yet durable homes, understanding the fundamentals of casting becomes vital. From the fundamental strategies to the elaborate information that can make or break a casting project, there is a wide range of insights and tips waiting to be found. As we venture into the world of light weight aluminum casting services, prepare to discover the essential elements that can shape the trajectory of your jobs and boost your understanding of this elaborate craft.
The Basics of Aluminum Spreading
What fundamental procedures are included in aluminum casting that create the foundation of this extensively made use of production method? Light weight aluminum casting is a affordable and functional technique utilized in different markets to develop facility and intricate steel parts. The procedure starts with the melting of aluminum ingots in a heater, typically at temperatures varying from 1220 ° F to 1670 ° F, relying on the specific light weight aluminum alloy being made use of. When molten, the aluminum is put right into a pre-designed mold and mildew tooth cavity, where it takes the form and strengthens of the mold.
After solidification, the mold and mildew is gotten rid of, and the casting undergoes finishing processes such as warm therapy, surface, and machining finishing to satisfy the needed requirements. Understanding these essential processes is necessary for attaining high-quality light weight aluminum spreadings with exact measurements and mechanical buildings.
Different Casting Techniques Discussed
Checking out the different strategies used in light weight aluminum casting provides useful insights into the diverse methods used to accomplish intricate and exact steel components. One typical approach is sand spreading, where a mold is created utilizing compacted sand around a pattern of the desired component. This method is flexible and affordable, ideal for both straightforward and complex shapes. An additional technique, die casting, involves injecting liquified light weight aluminum into a steel mold and mildew under high pressure. Die casting enables high precision and repeatability, making it excellent for automation of small to medium-sized parts. For more complex designs, investment spreading is commonly liked. This technique uses wax patterns that are disappeared, leaving a tooth cavity for the liquified aluminum to load. Investment spreading yields exact details and smooth coatings, making it popular in sectors like aerospace and automotive. Each casting technique has its unique benefits and is picked based on elements such as price, volume, and complexity considerations.
Factors to Think About When Choosing a Provider
When picking a light weight aluminum casting company, examining their experience and competence is important for making certain top quality and dependability in the production process. The carrier's experience in the area shows their experience with different spreading strategies, possible difficulties, and finest techniques. It is important to make inquiries concerning the types of projects they have worked with in the past, ensuring they straighten with the complexity why not try these out and specs of your very own task.
Furthermore, take into consideration the provider's reputation within the industry. Seek testimonials, endorsements, and instance researches that demonstrate their capacity to provide high-quality light weight aluminum castings continually. A reputable company will certainly often have accreditations or affiliations with sector great site companies, showcasing their dedication to quality and adherence to sector criteria.
Furthermore, evaluate the supplier's capacities in regards to customization, volume demands, and job timelines. Make sure that they can suit your specific demands and have the versatility to scale manufacturing as required. Efficient communication and transparency relating to prices, lead times, and high quality control procedures are also crucial elements to take into consideration when picking an aluminum spreading company.
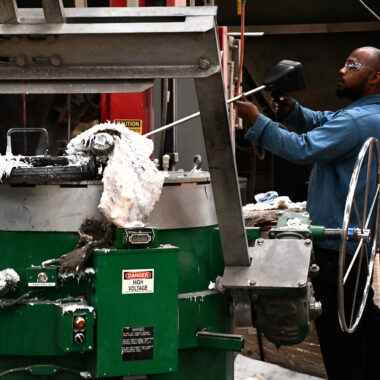
Common Obstacles and Solutions
Navigating with the complexities of aluminum spreading processes usually provides suppliers with a series of challenges that call for innovative options to ensure effectiveness and quality in manufacturing. One common challenge faced in light weight aluminum spreading is the formation of flaws such as porosity, contraction, or inclusions due to incorrect mold design or insufficient metal high quality.
Carrying out sophisticated innovations like computer-aided style (CAD) and computer numerical control (CNC) machining can enhance precision and uniformity in aluminum casting. By investing in automation and real-time surveillance systems, suppliers can enhance process control and reduce variations, ultimately boosting the general high quality of light weight aluminum actors products.
Tips for Optimizing Your Spreading Projects
To improve the effectiveness and quality of your aluminum casting projects, applying tactical optimization techniques is vital. One key idea for optimizing your casting projects is to carefully design eviction system. By making sure that the gating system is properly designed and appropriately put, you can improve the circulation of molten light weight aluminum and decrease the chances of issues in the last casting. Furthermore, utilizing computer system simulations can help in predicting and assessing the flow of metal throughout the casting procedure, permitting changes news to be made before actual production starts.

Conclusion
To conclude, recognizing the essentials of aluminum casting, various spreading methods, aspects to consider when choosing a carrier, typical obstacles and solutions, and tips for optimizing casting jobs are crucial for successful outcomes. By adhering to these understandings and implementing best individuals, practices and companies can make sure reliable and reliable aluminum spreading services that satisfy their certain requirements and demands.
Recognizing these fundamental processes is essential for achieving top quality aluminum spreadings with mechanical homes and exact dimensions.
When choosing a light weight aluminum casting service provider, evaluating their experience and proficiency is vital for ensuring top quality and dependability in the manufacturing procedure. Reliable communication and transparency concerning expenses, lead times, and top quality control procedures are also essential elements to consider when picking a light weight aluminum spreading solution company.
Navigating via the complexities of aluminum spreading procedures commonly offers suppliers with a series of challenges that require ingenious options to ensure effectiveness and top quality in production. One usual obstacle faced in light weight aluminum casting is the development of issues such as porosity, contraction, or additions due to inappropriate mold layout or inadequate steel high quality.
Report this page